Red Tags are a very useful tool as you begin to emphasize workplace organization and start to do an increasing number of continuous improvement projects.
-
Prevent disposing of necessary items
-
Provide a quick, easy, recognizable way to communicate with a team
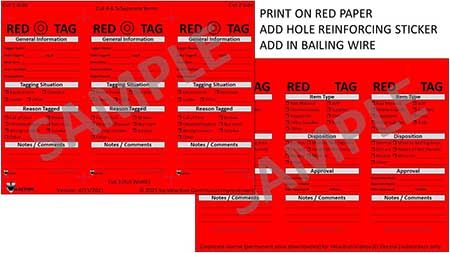
The best kaizen teams are cross-functional, meaning that they bring in outsiders who are familiar with continuous improvement, but may not be familiar with the process being improved. That gives them a fresh perspective so they can question things that people close to the process take for granted.
Unfortunately, that also means that most people on teams don't know what is needed in a work area, especially things that are used infrequently. (Note: Infrequently used tools that are not for general preventative maintenance should be questioned. They are red flags for problems.)
A Red Tag is simply placed on an item in question as an indicator that the team is considering removing it as part of the 5S effort. If nobody responds within a set period, the item can be safely removed from the work area.